How to Treat Aluminum PCB for Corrosion Resistance?
As aluminum PCBs are used more and more frequently in various high-stress environments and their corrosion resistance can directly affect their performance, many PCB users will ask us how to deal with their corrosion resistance when manufacturing aluminum PCBs. Then in this guide, we will introduce how to deal with the corrosion resistance of aluminum PCB.
Aluminum PCB material selection and its impact on corrosion resistance
The first step in ensuring corrosion resistance is choosing the right type of aluminum alloy. Then, the purity of the aluminum, alloying elements, and overall material quality all affect its corrosion susceptibility. For aluminum PCBs, alloys such as 5052-H32, 6061-T6, or 1060 are generally chosen. The excellent corrosion resistance 5052-H32 is particularly effective in saltwater environments, and 6061-T6 provides a good balance of strength, corrosion resistance, and weldability. It is often used in applications requiring thermal conductivity and mechanical strength. 1060 aluminum was chosen for its high thermal conductivity and excellent corrosion resistance, but it is softer and less durable than other alloys.
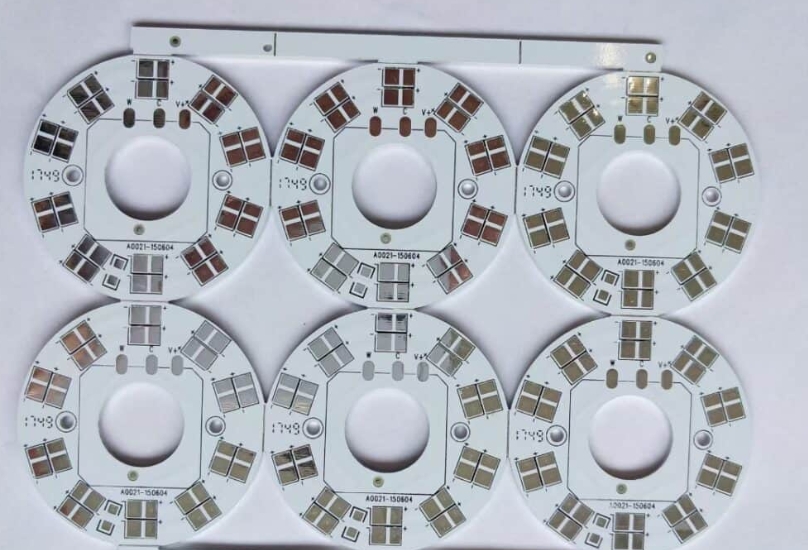
Protective coating for enhanced corrosion resistance of aluminum PCBs
The use of protective coatings is also one of the ways we enhance the corrosion resistance of aluminum PCBs. We use a variety of protective coatings including anodizing, organic polymer coatings, ceramic coatings, etc. Anodizing is one of the most popular and effective treatments for aluminum PCBs. It thickens the natural oxide layer on the surface of the aluminum substrate through an electrochemical process, thereby significantly enhancing its corrosion resistance. The anodized layer is non-conductive, preventing short circuits and reducing the risk of electrical failure.
Organic polymer coatings include various varnishes, paints, and other polymer materials such as acrylics, polyurethanes, and epoxy resins. These coatings are applied by spraying, dipping, or brushing to form a protective barrier on the aluminum surface. Ceramic coatings are advanced coatings with excellent corrosion resistance and high thermal stability. As a thin layer, ceramic coatings maintain their integrity under extreme temperature changes, which is particularly beneficial for high-temperature applications such as LED lighting systems and automotive electronics.
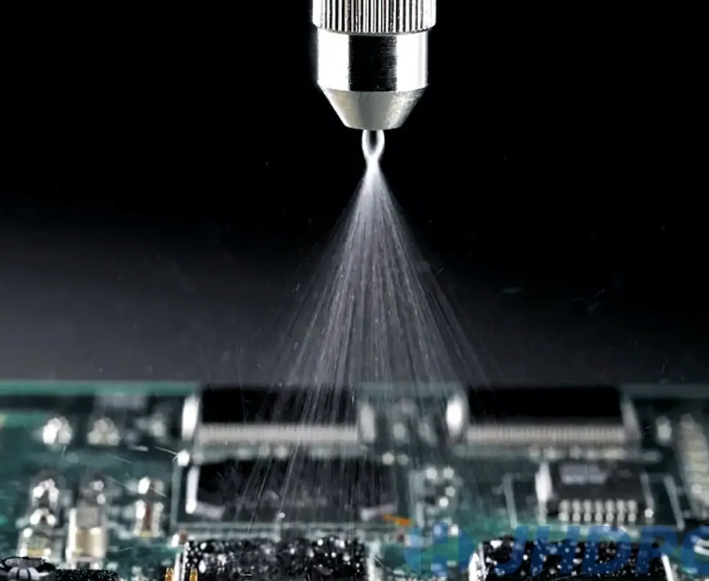
Surface treatment technology to prevent corrosion
Surface treatment technology plays a key role in protecting aluminum PCBs from corrosion. Techniques like anodizing enhance the natural oxide layer on aluminum, providing excellent protection against corrosion and wear. In addition, we will use surface treatment technologies such as HASL, ENIG, and OSP to improve solderability. They can also protect the exposed copper on the PCB from oxidation, thereby improving its performance.
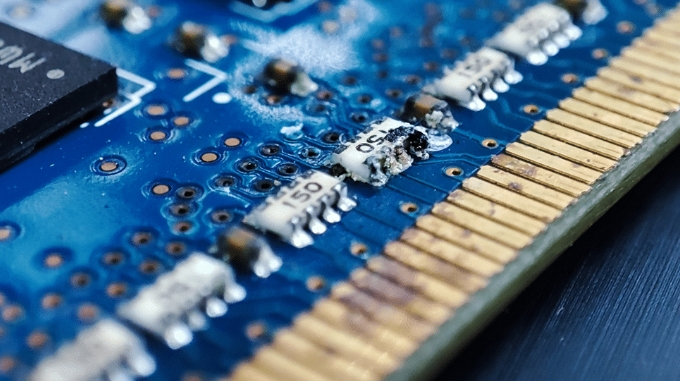
Environmental Considerations to Prevent Corrosion
The environment in which aluminum PCBs are used will also greatly affect their corrosion susceptibility. Therefore, you should avoid exposure to high humidity when using it. Use dehumidifiers, sealed enclosures, and air conditioning systems to maintain a controlled humidity environment if necessary. You must also avoid exposing aluminum PCBs to common industrial environments and ensure they are not near chemical storage or handling areas.
Routine inspection and maintenance
Routine inspection and maintenance are basic practices to maintain the corrosion resistance of aluminum PCBs. Regular visual inspection is required to keep white powdery spots or pits on the surface of aluminum PCBs. The inspection should also look for discoloration, deformation, or any other deformity that might indicate structural or environmental problems. Gently clean the PCB surface using a soft cloth and an appropriate non-corrosive cleaning solution. It is vital to ensure that the cleaning agent does not leave a residue that can cause corrosion. Depending on the results of the coating integrity check, the protective coating also needs to be reapplied periodically to ensure that areas of the PCB susceptible to environmental exposure are resealed to maintain the overall corrosion resistance of the assembly.
Ensure longevity through effective strategies
In short, we will maintain the corrosion resistance of aluminum PCBs and extend the service life of aluminum PCBs by selecting appropriate materials, corrosion-resistant protective coatings, anti-corrosion surface treatment techniques, and regular maintenance.