What to Consider When Selecting Double-Sided PCB for Industrial Applications
Double-sided PCB plays a pivotal role in many industrial applications. These boards offer greater routing flexibility by allowing components and traces on both sides of the board. For industries that demand compact designs and reliable connections, the Double-Sided PCB is a practical and efficient solution. Industrial environments often involve high voltages, mechanical stress, and extreme temperatures. Therefore, selecting the right Double-Sided PCB requires careful evaluation of performance, durability, and compatibility with specific operating conditions.
Evaluating Load and Power Requirements
When choosing a Double-Sided PCB for industrial use, understanding the load and power requirements is essential. These factors directly impact the board’s thickness, copper weight, and trace width. A mismatch here could cause overheating, circuit failures, or even irreversible damage to expensive systems.
Additionally, industries that rely on high-current systems, such as those in automation or motor control, must prioritise boards that can handle sustained power demands. By assessing electrical parameters early in the design process, engineers can select Double-Sided PCBs that guarantee both safety and optimal performance under continuous or peak load conditions. Taking time to analyse these needs can prevent future system malfunctions.
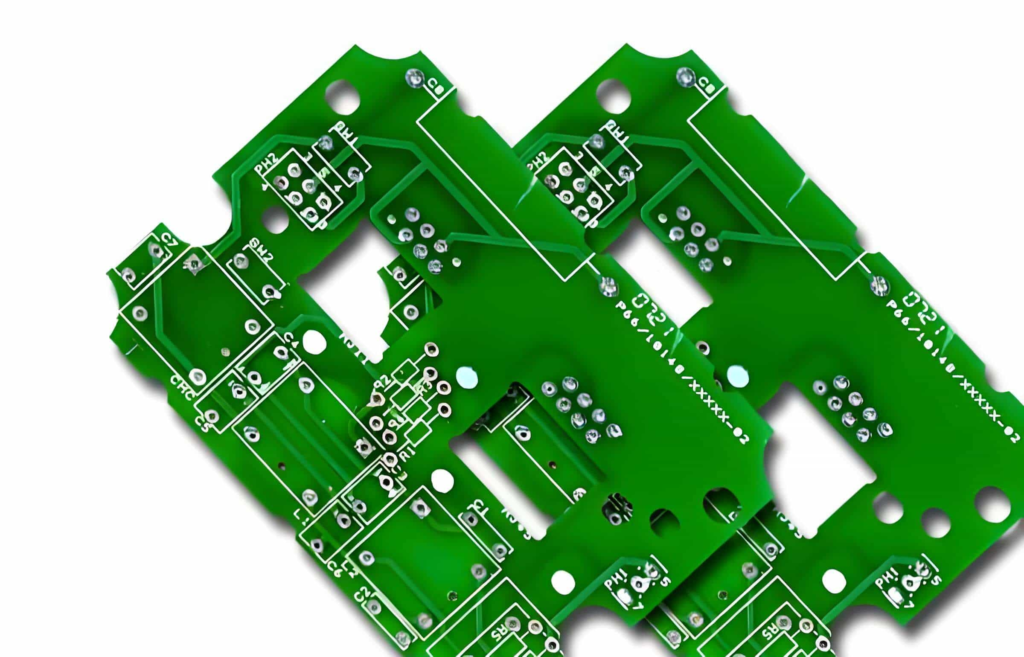
Material Selection for Harsh Environments
The choice of materials has a significant impact on the reliability of Double-Sided PCBs in industrial settings. FR4 is a standard base material, but advanced laminates may be required for high-temperature or chemically aggressive environments. Selecting the right substrate ensures long-term stability, even when exposed to continuous stress or environmental hazards.
In many cases, boards must withstand vibration, dust, and humidity without experiencing performance loss. Some industries even require flame-retardant or moisture-resistant properties for extra protection. Engineers should always align PCB materials with environmental demands. Doing so prevents premature failures and extends the service life of the PCB in harsh, high-risk applications, where failure isn’t an option.
Thermal Management and Heat Dissipation
Thermal management is a top priority for industrial PCBs. Excessive heat can damage both the board and the surrounding components. Double-sided PCB designs enable better heat distribution, particularly with thermal vias and thicker copper layers engineered to handle higher heat loads.
In high-power systems, engineers often utilise specialised coatings or heat sinks connected to the PCB for enhanced thermal control. Proper thermal analysis during the design stage ensures consistent temperatures during operation. By optimising heat dissipation, Double-Sided PCB enhances safety, prevents costly breakdowns, and provides the stability of entire systems under demanding conditions.
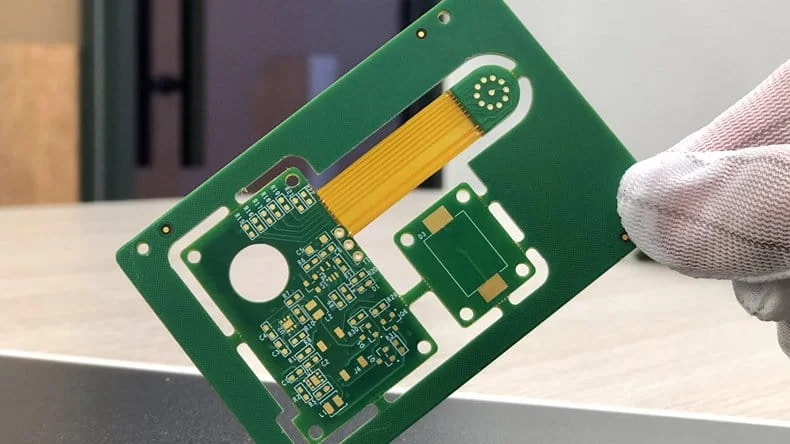
Layer Interconnect Reliability
Reliable interconnects between PCB layers are vital for industrial applications. Double-sided PCBs rely on plated through-holes (PTH) to connect circuits on both sides. The quality of these vias directly impacts signal integrity and overall electrical performance, especially in high-vibration environments.
Manufacturers must ensure precise drilling, plating thickness, and void-free connections throughout the production process. In high-vibration settings, reinforced vias or additional bonding techniques may also be necessary. Carefully designed interconnects guarantee consistent functionality throughout the product’s operational life, allowing companies to avoid unexpected failures and costly repairs.
Assembly and Component Placement Flexibility
Double-sided PCB offers more flexibility in assembly and component placement compared to single-sided boards. This is particularly useful in complex industrial systems where space optimisation is critical. Components can be placed on both sides to reduce board size while maintaining performance.
However, careful planning is essential to avoid assembly challenges or interference between components. Automated assembly processes, such as pick-and-place machines, work well with these designs when they’re optimised correctly. Well-planned layouts enhance manufacturability, lower production costs, and ensure robust electrical performance, ultimately supporting greater efficiency in industrial operations.
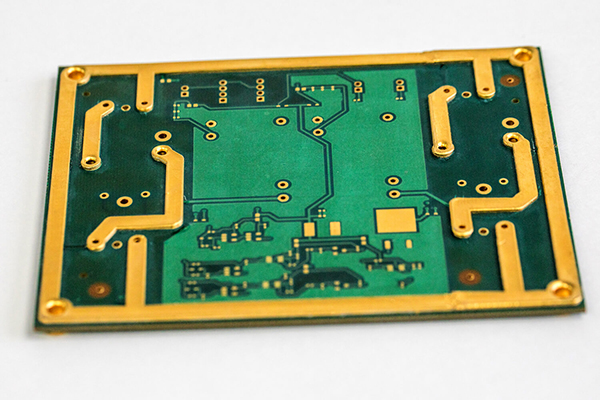
Testing and Quality Assurance Considerations
Rigorous testing is non-negotiable for Double-Sided PCBs in industrial applications. Testing procedures should include electrical testing, thermal cycling, and mechanical stress analysis. These tests verify that the PCB performs reliably under real-world conditions without compromising functionality.
Additionally, advanced inspection techniques such as automated optical inspection (AOI) and X-ray imaging help detect hidden defects in vias and solder joints. Ensuring proper quality control throughout manufacturing reduces the risk of future failures and strengthens product reliability. Investing in thorough testing upfront ultimately lowers long-term operational costs and enhances the board’s credibility in critical environments.
Key Factors in Choosing the Right Double-Sided PCB
Selecting the right Double-Sided PCB for industrial applications requires careful consideration of multiple technical factors. Engineers must evaluate power demands, materials, thermal management, interconnect reliability, and assembly needs during the design process. Each of these elements directly impacts the performance, durability, and operational stability of the board.