The Role of SSD PCB in NVMe and PCIe Based Drives?
The SSD PCB plays a pivotal role in enabling the performance and efficiency of modern NVMe and PCIe drives. Unlike traditional hard drives, which rely on spinning disks and mechanical arms, SSDs use NAND flash memory mounted on PCBs to store data. This transition from mechanical to solid-state architecture hinges on the quality and layout of the printed circuit board. Every component, from the controller to the memory chips, must be precisely arranged to ensure high-speed data transfer and thermal stability.
Architectural Layout and Signal Integrity
The design of an SSD PCB must support high-speed data transfers with minimal signal degradation to ensure optimal performance. With NVMe and PCIe protocols demanding faster speeds, signal integrity becomes a critical design consideration. Engineers use differential pair routing and impedance matching to ensure reliable communication between the controller and NAND chips. Even minor imperfections in trace geometry can introduce latency or errors.
Additionally, multilayer PCBs are often employed to separate power and signal layers. This layout helps reduce crosstalk and enhances thermal performance. Advanced techniques, such as microvias and via-in-pad, further optimize space while maintaining robust connections. Without meticulous planning of the PCB architecture, the full potential of NVMe or PCIe drives cannot be realized. Therefore, the SSD PCB has a direct impact on drive responsiveness and reliability.
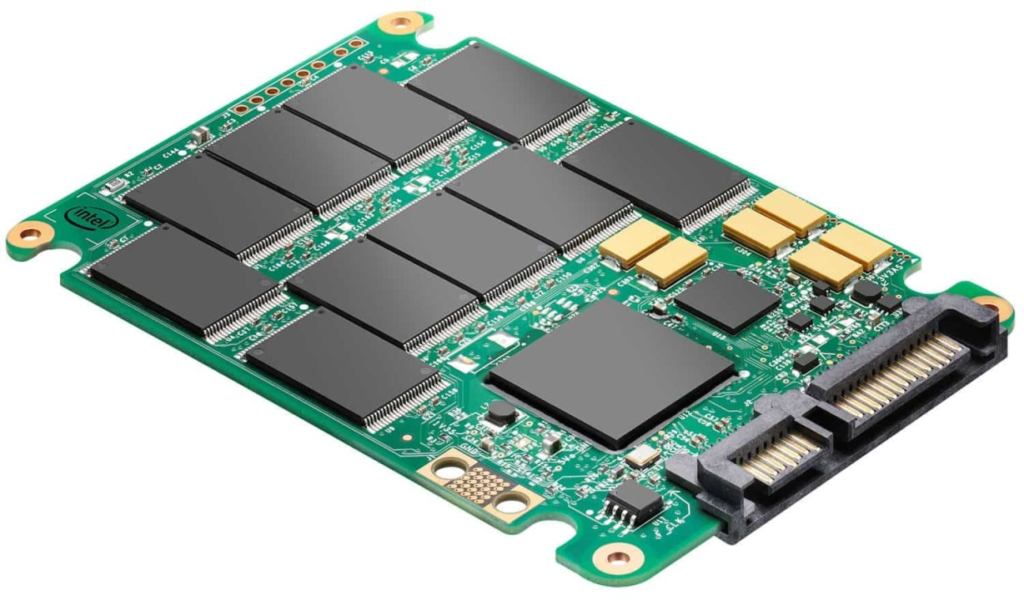
Power Distribution and Heat Management
One of the unsung heroes of SSD performance is power delivery. A well-designed SSD PCB ensures stable voltage levels for each component, from the controller to DRAM and NAND cells. Any fluctuation in power delivery can cause system instability or data corruption. Thus, engineers integrate power planes, decoupling capacitors, and voltage regulators to maintain balance.
Equally important is thermal management. As drive speeds increase, so does the generation of heat. SSD PCBs use copper pours and thermal vias to dissipate heat away from sensitive areas. Some high-performance drives even include integrated heat spreaders or copper shims to enhance cooling efficiency. The PCB acts as the foundation for these cooling mechanisms. Efficient power and thermal management, therefore, are essential for sustaining peak performance in NVMe and PCIe applications.
Compatibility with Controller Technologies
Modern SSD controllers handle complex functions such as wear levelling, error correction, and garbage collection. For these features to work efficiently, the SSD PCB must accommodate the controller’s pin configuration and communication protocols. PCB design also needs to support multiple NAND interfaces, such as Toggle, ONFI, or NV-DDR.
Moreover, SSD PCBs may support either DRAM or DRAM-less configurations, which in turn affects data mapping and performance. In DRAM-less designs, the Host Memory Buffer (HMB) relies on efficient signal routing and low-latency paths to achieve its functionality. Therefore, compatibility with the controller’s architecture is paramount. Without a well-matched PCB, even the most advanced controller cannot perform optimally.
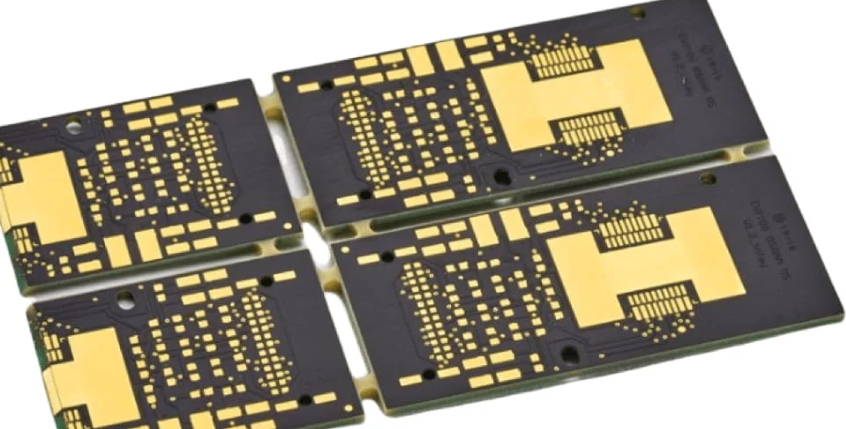
Form Factor Optimization for Compact Designs
Space-saving designs are a hallmark of modern electronics, and SSDs are no exception. NVMe drives are often used in ultrabooks and compact desktops, requiring SSD PCBs to be incredibly compact yet powerful. Engineers must fit multiple components into tight spaces without sacrificing performance.
To achieve this, SSD PCBs employ techniques such as double-sided mounting and multi-layer stacking. These strategies enable the placement of more components within a smaller footprint. However, smaller PCBs often face higher risks of thermal and electromagnetic interference. As a result, the design process requires striking a balance between size, performance, and durability. Compact SSD PCBs are a testament to how innovation in board design meets the needs of space-constrained applications.
Reliability and Longevity Under Stress
Reliability is a critical aspect of storage devices, especially those used in enterprise or industrial settings. The SSD PCB contributes directly to the drive’s durability by ensuring solid electrical connections, optimal power flow, and minimal signal loss. High-quality materials, such as FR4, polyimide, or even ceramic, are selected based on environmental requirements.
In high-vibration or high-temperature environments, PCB robustness becomes even more vital. Reinforced mounting points, conformal coatings, and solder joint integrity ensure that the drive performs under stress. As SSDs often serve as primary boot or storage devices, failures can be catastrophic. Hence, the SSD PCB must be engineered for long-term reliability, especially in mission-critical systems.
.png)
Role in Data Security and Error Handling
Security and data integrity are increasingly important in modern storage. The SSD PCB houses hardware encryption modules and interfaces that support TCG Opal or IEEE 1667 standards. Proper layout ensures that encryption hardware communicates effectively with the controller and NAND.
Additionally, error-handling features such as ECC (Error Correction Code) require precise signal timing and robust signal paths. The SSD PCB supports these processes by minimizing jitter and ensuring electrical stability. Together, these features protect sensitive data from loss or corruption. As data breaches become more common, a secure and well-designed PCB is essential for protecting digital assets.
Integration with Emerging Technologies
The SSD landscape is rapidly evolving. With PCIe 5.0 and new NVMe specifications on the horizon, SSD PCBs must evolve too. Advanced materials, such as low-loss laminates and refined manufacturing processes, enable the meeting of higher frequencies and tighter tolerances.
Furthermore, SSD PCBs are increasingly designed to support AI workloads, edge computing, and other data-intensive tasks. These applications require higher IOPS and lower latency, which can only be delivered through sophisticated PCB design. The integration of these new technologies demands a future-proof PCB architecture. Engineers must think ahead to keep pace with technology shifts.
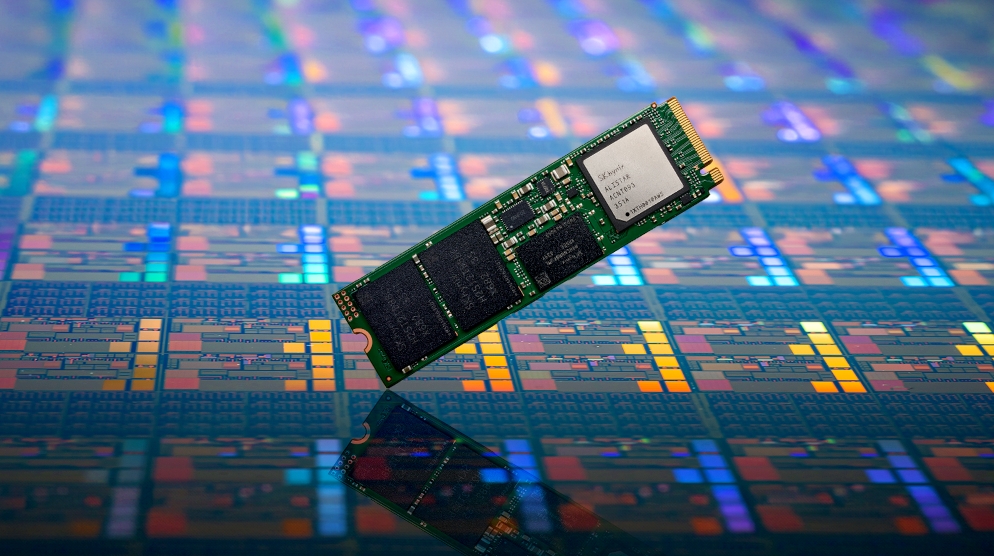
SSD PCB as the Backbone of Performance
The SSD PCB is not just a platform for mounting chips; it is the core that defines performance, reliability, and scalability. From supporting advanced controllers to enabling fast NVMe and PCIe communication, every aspect of the SSD depends on PCB design. The better the board, the better the drive.