How Ceramic PCB Supports Miniaturization in Advanced Electronic Devices?
From wearables to military drones, everything is shrinking in size while performance expectations are skyrocketing. The Ceramic PCB. Unlike traditional circuit boards, ceramic substrates can withstand extreme temperatures, withstand high power densities, and enable tight circuit integration. As advanced devices shrink in size, so do tolerances. Ceramic PCBs have superior dimensional stability and thermal conductivity, allowing engineers to reduce package size without compromising reliability.
Material Science Meets Engineering Demands
At the core of every Ceramic PCB lies a choice of materials—typically aluminium oxide, aluminium nitride, or silicon carbide. Each brings its own thermal, electrical, and mechanical properties to the table. These materials don’t just pass current—they survive it.
Engineers face a dilemma: More features mean more heat, but smaller sizes leave no room for heatsinks. That’s where ceramic substrates shine. Their ability to dissipate heat internally eliminates bulky cooling solutions. It’s not just science—it’s elegant engineering. And when design constraints meet ceramic logic, innovation happens.
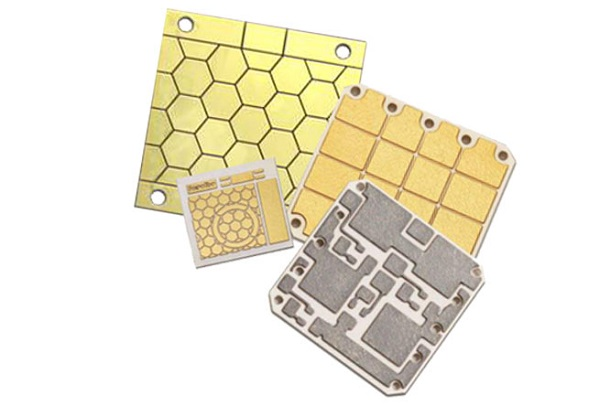
Power Density Without the Pain
As IoT and 5G devices multiply, power density becomes a design bottleneck. Traditional FR4 PCBs can’t cope. Ceramic PCBs allow circuits to be packed tightly, layered more efficiently, and driven harder, without thermal runaway.
This density gain translates into smaller form factors and more compact devices. Think of medical implants that don’t bulge under the skin or drones with longer flight times due to weight reduction. With ceramic substrates, engineers don’t ask “Can it be done?”—they ask “How fast can we ship it?”
Thermal Management Becomes Invisible
In high-reliability systems—like satellites or autonomous vehicles—heat is a killer. Ceramic PCBs turn thermal management from an afterthought into an intrinsic advantage. They channel heat like a conductor channels music—precisely, gracefully, and with zero distortion.
Forget fans and clunky cooling blocks. With ceramics, the board itself becomes the heat sink. This shift enables designers to focus on performance, not thermal compromise. Less clutter. Fewer points of failure. More room for real innovation.
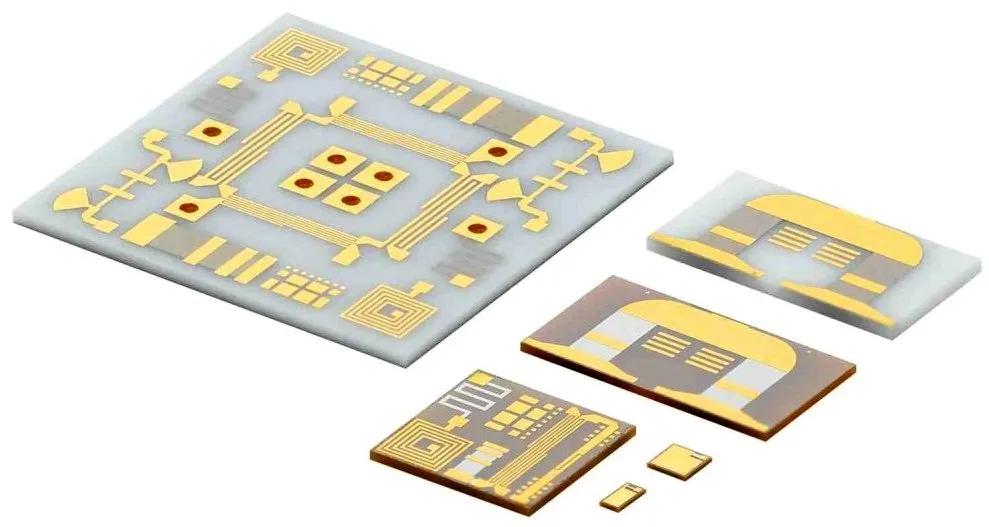
Precision at the Microscopic Level
Miniaturization doesn’t tolerate error. Even minor warping or expansion can cause catastrophic failure. That’s why Ceramic PCB technology is often used in aerospace, military, and medical applications where failure is not an option.
Ceramic’s ultra-low thermal expansion ensures micron-level accuracy in multilayer stacks. That translates into tighter tolerances and higher signal integrity, even under stress. Put: when everything else shrinks, precision becomes priceless—and ceramics deliver it in spades.
Signal Integrity in the Era of Noise
As circuits shrink and frequencies rise, signal integrity becomes a battlefield. Electromagnetic interference, crosstalk, and latency plague traditional boards. Ceramic PCBs, with their low dielectric loss and consistent impedance, offer a stable canvas for high-speed signals.
In RF modules, phased arrays, or high-frequency processors, ceramic substrates enable better wave propagation and cleaner signals. They’re not just boards—they’re enablers of clarity in an increasingly noisy world. For devices operating in GHz territory, ceramic is the difference between excellence and failure.
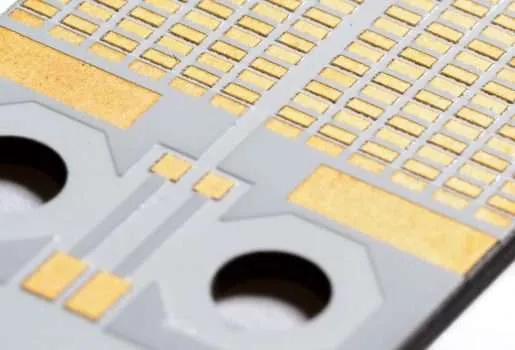
Manufacturing That Keeps Pace with Design
Advanced devices require precision manufacturing. The good news? Ceramic PCB production has evolved, too. Techniques like laser drilling, DPC (Direct Plated Copper), and LTCC (Low Temperature Co-fired Ceramic) support complex geometries and multilayer builds without sacrificing reliability.
This manufacturing maturity means engineers can iterate faster, prototype bolder, and scale with confidence. Moreover, ceramic PCBs are more compatible with modern SMT processes and increasingly recyclable. They’re not just built for devices—they’re built for future ecosystems.
Ceramic PCB Redefine What’s Possible in Small Spaces
Ceramic PCBs deliver superior performance in a tiny package. They enable designers to break through previous limitations of heat, space, and precision to create surprising and durable products. Whether it’s biosensors, high-speed chipsets, or next-generation satellite modules, ceramic boards keep technology moving forward. In the age of miniaturization, they are not only essential but indispensable.