Looking for Durable High-Temp PCBs? Try Our Custom Ceramic PCB Solutions
Standard PCBS often struggle to deliver consistent performance in high-temperature environments. That’s where ceramic PCBS prove their value. Designed to resist warping, delamination, and conductivity loss, these boards thrive under extreme conditions—often above 250°C. Ceramic PCBS offer unmatched thermal stability and durability, from aerospace to automotive electronics. If you’re seeking reliable high-temperature PCB solutions, explore our advanced ceramic PCB offerings tailored for demanding applications.
Understanding the Unique Material Advantages of Ceramic PCB
One of the primary reasons for considering ceramic PCBs is their inherent material strength. Unlike polymer-based substrates, ceramics can resist both heat and mechanical stress. Engineers can design for higher performance without worrying about heat damage or board expansion.
Another critical advantage is the low coefficient of thermal expansion (CTE). Ceramic substrates expand far less than FR4, making them compatible with other high-precision components. These physical properties ensure minimal distortion, essential in fields like RF communication, where signal integrity is crucial. Simply put, Ceramic PCBs offer superior form and function.
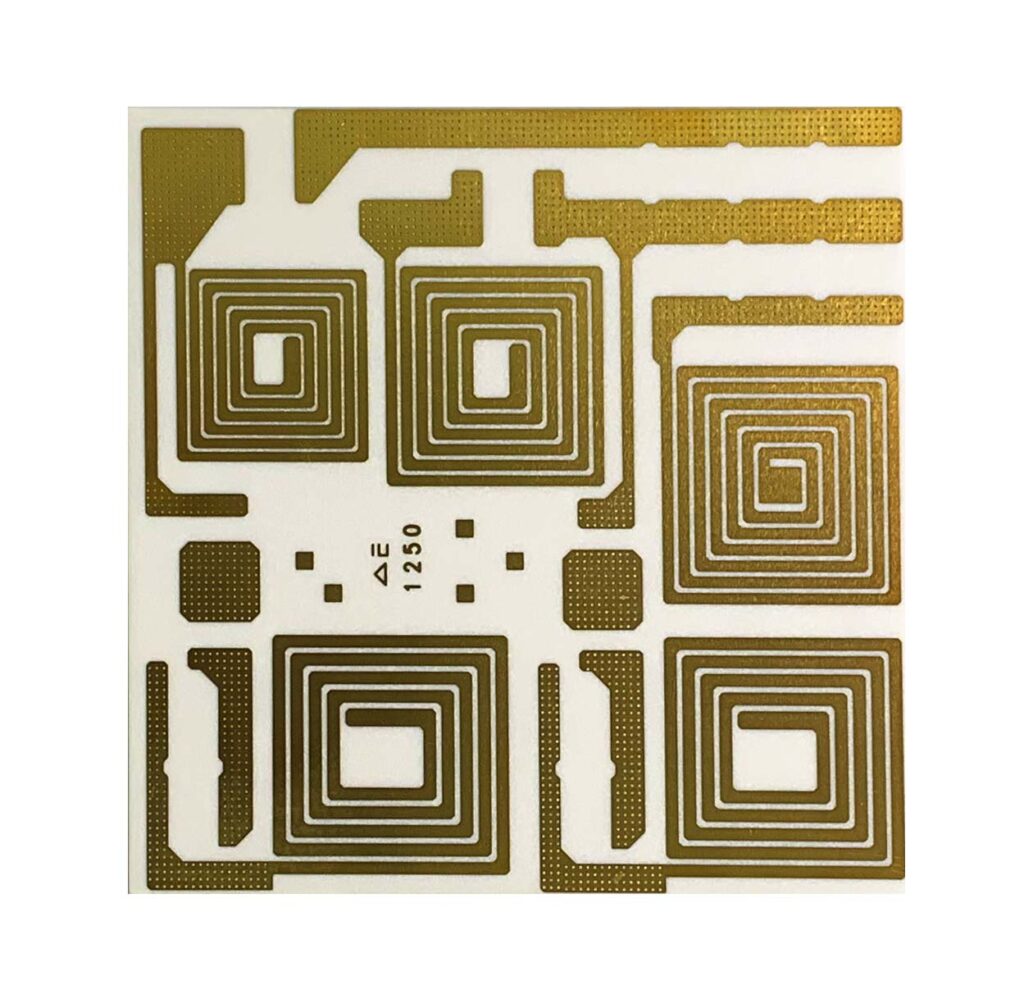
Thermal Management and Heat Dissipation Made Easy
Effective heat dissipation is a cornerstone of PCB reliability. Ceramic PCBs shine here, thanks to their thermal conductivity, ranging from 20 W/mK to over 180 W/mK, depending on the material used. This dramatically reduces the risk of hot spots and thermal fatigue.
This high thermal conductivity also requires fewer heat sinks and cooling mechanisms. The result? Lower system costs and simplified assembly. Whether dealing with power electronics or LED lighting systems, using a Ceramic PCB allows you to optimize thermal management and design footprints.
Aerospace and Automotive Applications That Demand Ceramic PCB
Both the aerospace and automotive sectors operate under harsh environmental conditions. Components in these industries must survive high altitudes, intense vibrations, and massive temperature swings. Ceramic PCBs are frequently the backbone of these applications due to their ruggedness and reliability.
In satellites and aircraft, weight and reliability are paramount. Ceramic PCBs provide an excellent balance between lightweight design and thermal robustness. Meanwhile, Ceramic PCBs ensure critical systems remain operational in automotive electronics like power converters and engine control units, even under the hood.
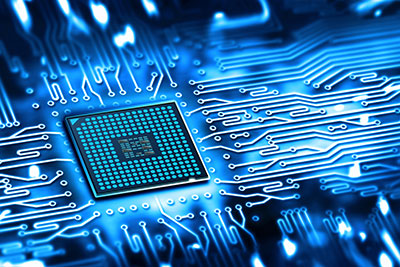
Custom Design Flexibility for Complex Requirements
We understand that off-the-shelf solutions don’t always meet your technical requirements. That’s why we offer fully custom Ceramic PCB manufacturing tailored to your application. Whether it’s multilayer layouts, complex trace patterns, or embedded components, our engineering team supports your design vision from prototype to production.
Moreover, we utilize advanced fabrication technologies such as laser drilling and metallization. These enable tighter tolerances and higher routing density. Our clients often find that switching to custom Ceramic PCBs improves reliability and simplifies their overall design architecture.
Comparing Ceramic PCBs to Other High-Performance Materials
You may wonder how Ceramic PCBs stack up against other advanced materials. While metals like copper-core PCBs offer high thermal performance, they fall short in electrical insulation. Ceramics provide the best of both worlds: excellent heat dissipation and superior dielectric strength.
Polyimide boards are another alternative, often used in flexible circuits. However, they can’t match ceramic substrates’ dimensional stability and rigidity. Ceramic PCBs are the logical choice if your design requires long-term reliability under continuous thermal and mechanical stress.
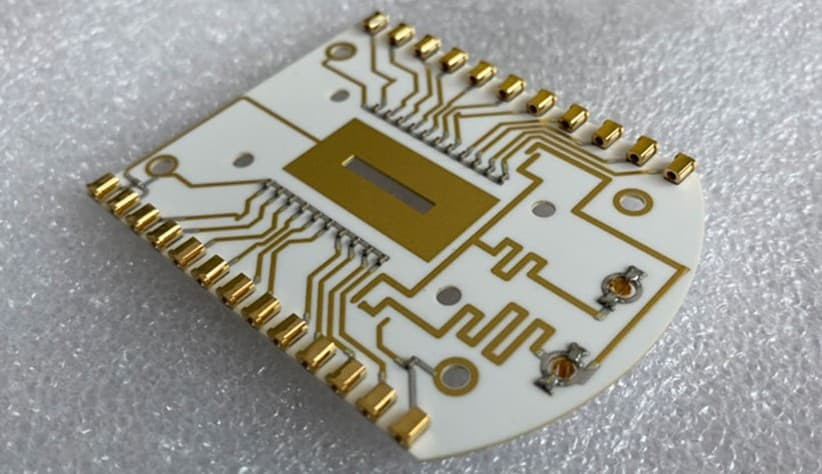
Quality Control and Manufacturing Precision You Can Trust
We don’t just manufacture Ceramic PCBs; we perfect them. Our process includes rigorous quality control protocols like X-ray inspection, thermal cycling tests, and dimensional verification. These steps ensure that each board meets industry standards and performs consistently in real-world conditions.
In addition to quality assurance, we invest in staff training and equipment upgrades to keep pace with evolving technology. Whether you’re ordering 10 units or 10,000, our precision manufacturing process ensures uniformity, which is key to system performance and reliability.
Invest in a Custom Ceramic PCB Today
Choosing a Ceramic PCB is not just a technical decision—it’s a strategic one. These PCBs offer unmatched durability, performance, and reliability. As industries increasingly rely on more intelligent, compact systems, Ceramic PCBs provide the foundational support needed to build next-gen products.
So if you’re searching for a durable, high-temperature solution, our custom Ceramic PCB offerings deliver on every front. From prototyping to full-scale production, we partner with you at every stage to ensure success. Future-proof your design today with a custom Ceramic PCB that exceeds expectations.